Ceramic Protective Coatings
Ultramet applies protective coatings to carbon/carbon and ceramic matrix composites, graphite, refractory metals, and superalloys for operation in severe environments. Low temperature deposition (<752°F [400°C]) is possible to accommodate components with low melting points.
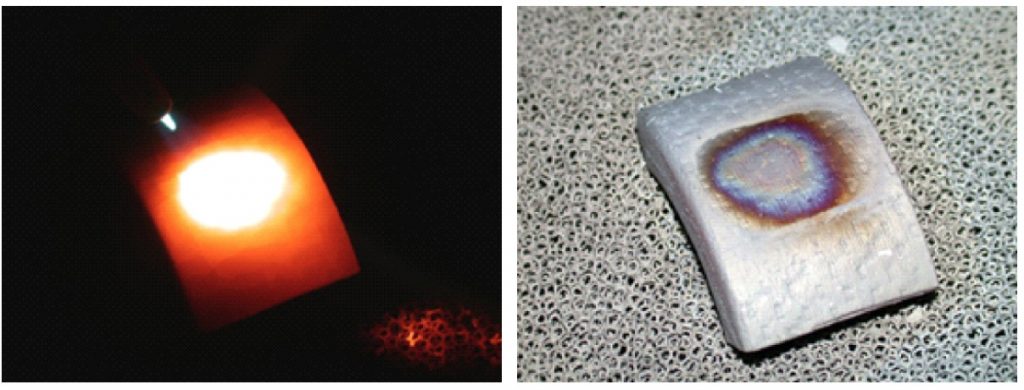
Photographs of carbon/carbon coupon coated with layered hafnium carbide/silicon carbide during and after oxyacetylene torch testing
Advantages of Ceramic Protective Coatings
- High temperature oxidation protection for refractory metal-, ceramic-, and carbon-based components
- Deposition at temperatures as low as 10% of the melting point of the coating material
- No porosity (fully dense)
- Availability in various metal carbides, oxides, nitrides, and borides
- High emissivity
- Thermal protection
- Applicability to intricate shapes and textured surfaces
Applications of Ceramic Protective Coatings
- Engine and airframe components
- Fiber interface coatings
- Thermal protection system components