Chemical Vapor Deposition (CVD)
CVD results from the chemical reaction of gaseous precursor(s) at a heated substrate to yield a fully dense deposit. Ultramet uses chemical Vapor Deposition to apply refractory metals and ceramics as thin coatings on various substrates and to produce freestanding thick-walled structures.
Thermodynamics and kinetics drive both precursor generation and decomposition. Control of thermodynamics and kinetics through temperature, pressure, and concentrations yields the desired deposit.
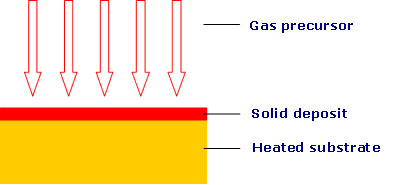
CVD reaction
Metal deposition
metal halide (g) → metal(s) + byproduct (g)
Ceramic deposition
metal halide (g) + oxygen/carbon/nitrogen/boron source (g) → ceramic(s) + byproduct (g)
Advantages of Chemical Vapor Deposition (CVD)
- Can be used for a wide range of metals and ceramics
- Can be used for CVD coatings or freestanding structures
- Fabricates net or near-net complex shapes
- Is self-cleaning—extremely high purity deposits (>99.995% purity)
- Conforms homogeneously to contours of substrate surface
- Has near-theoretical as-deposited density
- Has controllable thickness and morphology
- Forms alloys
- Infiltrates fiber preforms and foam structures
- Coats internal passages with high length-to-diameter ratios
- Can simultaneously coat multiple components
- Coats powders
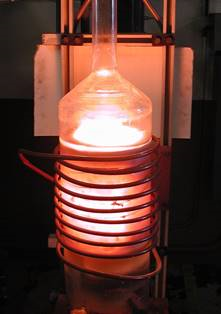
Hot-wall CVD reactor in process. Parts heated and coated within graphite furnace.
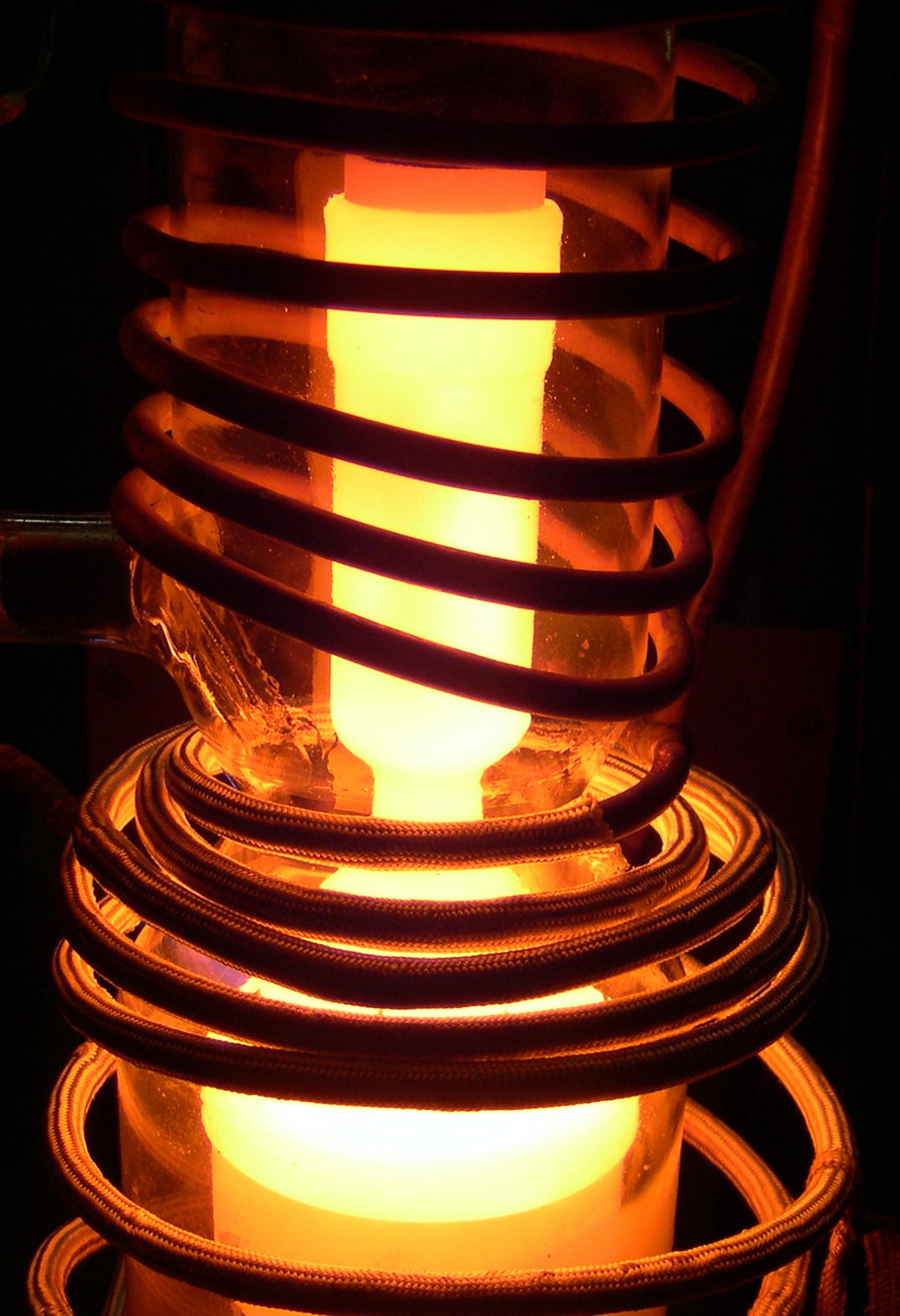
Cold-wall CVD reactor in process. Part heated directly and coated.
Microstructure of high-emittance black rhenium coating showing pyramidal dendrites formed by CVD
Layered CVD ceramic coating (top) conforms closely to underlying substrate to create a robust bond at the interface.
Left, large freestanding solid rhenium thruster (19″ high × 10″ diameter at base) fabricated by CVD, demonstrating Ultramet’s scale-up expertise; top right, freestanding parts of solid rhenium, tantalum, and tungsten formed by CVD; bottom right, monolithic CVD rhenium thrust chambers for tactical propulsion applications.
Top left, mirror fabricated entirely by CVD of silicon carbide foam with a polished silicon carbide facesheet; bottom left, rhenium-coated graphite spheres; right, iridium-lined rhenium thrust chamber with niobium flanges, all fabricated by CVD.
CVI
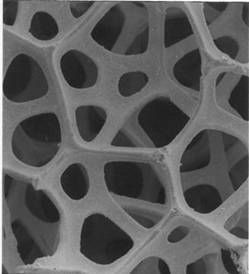
Rhenium foam fabricated by CVI, showing uniform coating and open-cell structure
Chemical vapor infiltration (CVI) is CVD with minor process changes that allow homogenous infiltration of porous structures such as foams and fiber preforms. Through control of pressure and/or thermal gradients within a reactor, gaseous precursors are allowed to uniformly permeate porous structures. Deposition of the desired compound thus occurs on all internal surfaces. CVI offers the ability to fabricate engineered porous structures such as reticulated foam from any of the materials that can be deposited via CVD.
UVCVD
Ultraviolet-activated chemical vapor deposition (UVCVD) is a variant of CVD that uses ultraviolet energy to drive the chemical reaction instead of thermal energy. The primary advantage of UVCVD is the ability to apply CVD coatings at extremely low temperatures (room temperature to 300°C).
Ultramet specializes in the chemical vapor deposition of refractory metals and ceramics. CVD results from the chemical reaction of gaseous precursor(s) at a heated substrate to yield a fully dense deposit. Ultramet uses chemical vapor deposition to apply refractory metals and ceramics as thin coatings on various substrates and to produce freestanding thick-walled structures. Please contact us for your specific needs and applications. The following are some of the materials with which Ultramet possesses broad experience:
Nonoxide ceramics
Tantalum carbide (TaC)
Tantalum nitride (TaN)
Tantalum diboride (TaB2)
Tungsten carbide (WC)
Tungsten diboride (WB2)
Hafnium carbide (HfC)
Hafnium nitride (HfN)
Hafnium diboride (HfB2)
Zirconium carbide (ZrC)
Zirconium nitride (ZrN)
Zirconium diboride (ZrB2)
Silicon carbide (SiC)
Silicon nitride (Si3Ni4)
Niobium carbide (NbC)
Niobium nitride (NbN)
Niobium diboride (NbB2)
Titanium carbide (TiC)
Titanium nitride (TiN)
Titanium diboride (TiB2)
Vanadium carbide (VC)
Vanadium nitride (VN)
Boron carbide (B4C)
Boron nitride (BN)
Metals
Rhenium (Re)
Tantalum (Ta)
Tungsten (W)
Niobium (Nb)
Molybdenum (Mo)
Iridium (Ir)
Platinum (Pt)
Boron (B)
Silicon (Si)
Metal alloys: W-Re, Ta-W,
Mo-Re, Ir-Pt
Oxide ceramics
Alumina (Al2O3)
Hafnia (HfO2)
Silica (SiO2)
Tantala (Ta2O5)
Titania (TiO2)
Yttria (Y2O3)
Zirconia (ZrO2)
Chemical Vapor Deposition (CVD) Process
- Fabricate mandrel that conforms to inner dimensions of final component.
- Deposit desired material(s).
- Remove mandrel to yield final part.
Chemical Vapor Deposition (CVD) Advantages
- Can deposit several materials to form a composite or lined structure
- Can fabricate components with intricate inner geometries
- Yields net-shape parts, requiring little or no postprocess machining
